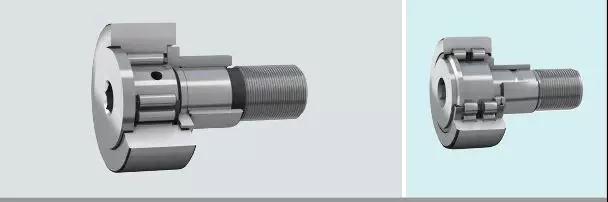
Whether you use cam follower bearings for cam followers, or for track, guide, or support rollers, their performance depends largely on the type you select. Important factors include loads, speeds, misalignment, installation, and lubrication.
Cam follower bearings are used mainly in three types of applications: following the surface of a cam, supporting linear motion components, or laterally locating components during linear movement.
Of these, cam follower applications range from simple two-dimensional cams to complex three-dimensional indexing cams with multiple followers.
Linear motion support applications include platform support rollers and die transfer rollers. Supporting a linear motion component with cam follower bearings reduces sliding friction and track wear. By reducing wear, it also helps maintain precise machine motion. Plus, cam follower bearings guide linear motion components in lateral as well as vertical directions.
Basic types
Cam follower types include standard stud, heavy stud, and yoke. Both stud types are mounted cantilever-style on a support housing. The heavy stud version is used for heavy loads, shock loading, or applications requiring minimal deflection. Except for the stud diameter and end plate design, standard and heavy stud versions are essentially the same.
The yoke version mounts on a pin with a straddle or yoke support arrangement. Because yoke mounting distributes load more uniformly over the bearing, the limit or working load rating for a yoke type follower is generally equal to that of a heavy stud follower.
Most cam followers contain needle bearings. These bearings generally handle radial loads only, not thrust or axial loads. Other followers use either cylindrical or tapered roller bearings, or ball bearings. The cylindrical types contain double-row cylindrical roller bearings that handle higher loads and speeds plus light thrust loads.
Units with ball bearings or tapered roller bearings handle combined radial and thrust loads. Such units typically use double-row ball bearings for roller ODs less than 3 in., and double-row tapered roller bearings for ODs 3 in. and larger. They generally have seals and large lubricant reservoirs for operation in dirty environments.
These bearing types (mainly ball and tapered roller) come with various roller configurations, so they can ride on different types of tracks or perform different functions. The cylindrical OD type operates on a flat track or cam similar to needle bearing followers. The flanged OD provides axial location. The Vshaped OD operates on special “V” tracks, square or round bar, or even angle-iron tracks. And the Ugrooved OD unit usually operates as a wire straightener bearing.
Optional features
If the standard cam follower bearings don’t meet your needs, several options are available to help you adapt them for special applications.
Seals. The seal improves bearing life by keeping contaminants out and lubricant in. Some types are made of molyfilled nylon to reduce friction between the roller and the end plate or flange. This type of seal fits on the end plate or flange OD and provides a closerunning labyrinth sealing effect with the roller. By separating the rotating roller counterbore faces from the end plate or flange, the seal eliminates sliding metalto- metal contact. The resulting lower operating temperatures reduce lubrication requirements and permit higher operating speeds. Generally, lubrication frequency can be cut to about one-third that of conventional cam followers.
Crowned OD. An optional crown on the outer roller OD, compensates for small amounts of misalignment between the cam follower and the track or cam. This helps prevent corner loading of the roller and reduces thrust loads on the bearing. The crowned OD also reduces thrust loading in applications involving circular motion, such as a turntable support.
Hex hole.Stud type bearings are usually supplied with a screwdriver slot, which lets you hold the stud while tightening the mounting nuts. An optional hex socket hole in either the roller or stud end of the bearing accommodates a standard hex-head wrench, which has more holding power. In small bearings, however, a hex hole in the roller end of the bearing may replace a relubrication hole.
Eccentric stud.An eccentric stud bearing, lets you adjust the radial position of the bearing relative to its support housing for applications requiring load sharing or radial preload. This option is most useful where several cam follower bearings support a load, and mounting inaccuracies prevent standard bearings from equally sharing the load. The eccentric adjustment feature can also compensate for cam or track wear.
Retainer.Bearings with rolling element retainers, are used in applications requiring higher speeds or longer prelubricated life (see manufacturer’s catalog). This option reduces internal friction and provides a larger grease reservoir than that in a conventional needle bearing. However, load capacity is less than that of the conventional needle bearing because there are fewer rolling elements and they are shorter.
Self-lubricating bushing.The self-lubricating bushing is best suited for low-speed applications where relubrication is undesirable. Here, a plastic bushing replaces the set of needle rollers used in a standard bearing. The life of a bushing type unit depends upon the amount of internal wear acceptable in the specific application. Where feasible, a continuous oil supply can be used to extend bushing life.
Selection factors
To select a cam follower bearing for a cam or track system, consider the load magnitude and type, speed, deflection, misalignment, and lubrication.
Loads, speeds, and life requirements.Load magnitude (and direction) affects the selection of both bearing size and type. For stud cam follower bearings, the stud strength and deflection limits determine load capacity. To calculate bearing life, especially for systems with varying loads, consult the manufacturer’s literature, bearing text books, and computer programs.
Applications involving both radial and axial loads usually require ball or tapered roller bearings. Be wary of shock loading, which can damage the outer roller, and produce brinelling (permanent deformation of races and rolling elements) that, in turn, causes vibration.
Speed limits are a major factor in selecting a bearing type. Needle bearing cam followers usually have the lowest speed limit. Higher speeds are achieved with caged needle bearings, and cylindrical or tapered roller bearings. Ball bearing units handle the highest speeds because of their low internal friction. Consult the manufacturer to obtain speed limits for specific applications.
Misalignment and deflection. Crowned rollers reduce the stresses caused by angular misalignment between a cam follower and a cam, but these rollers require increasing the track capacity by about 20% to accommodate the resulting point contact.
A cantilever-mounted stud deflects under load. Factors that affect the amount of deflection include the corner radius in the stud support housing, the fit between support housing and stud, and the housing material. To reduce this deflection, use a heavy stud or yokemounted unit. For applications that impose deflections and subsequent thrust loading beyond the capability of a needle bearing, use a cylindrical or tapered roller bearing, or a ball bearing to accommodate the thrust loading.
Lubrication. Oil is the preferred lubricant in high-speed cam applications because it cools a bearing more effectively and does not deteriorate as fast as grease. Oil is usually applied to bearings by the splash method.
Grease is suitable for slow-speed cam and track applications. Most stud type cam followers are supplied prepacked with a lithium-soap or soda-calcium grease, which is applied through a lubrication hole in either end of the stud. For yoke type bearings, apply grease through the mounting pin.
The oil, or oil carried by the grease, should have a viscosity of 100 SSU at the bearing operating temperature. Speed is the major factor influencing operating temperature, but loading also affects the temperature. To estimate operating temperature, compare actual speeds and loads to limiting speeds and dynamic load ratings recommended by manufacturers. Temperature limits for greases usually range from 225 to 250 F. For prolonged operation, keep the temperature at least 50 F lower.
Lubrication intervals depend on the application. Bearings exposed to extreme contamination, such as washdown conditions, may need daily lubrication. In clean environments, however, bearings may run a year or more before relubrication. Some cam followers can’t be relubricated, but they usually have more effective seals and large grease reservoirs.
Selecting cam or track hardness
Obtaining the proper cam or track surface hardness can be as important as finding the right bearing size. A cam or track of insufficient hardness will wear or plastically deform under load.
Where dimensional accuracy is not critical, you can use soft materials to reduce costs. For example, the work hardening of low-carbon steel, accompanied by small amounts of wear-in of the bearing on the track surface can produce satisfactory performance. For more precise applications, use hardened track and cam surfaces, up to 60 HRC, to minimize wear.
The capacity of a steel track (the bearing load that it withstands without plastic deformation of its surface) depends on the bearing size as well as the track strength and hardness. Track capacities for specific cam follower bearings are available from bearing manufacturers.
Cam and track surfaces are often difficult to keep lubricated, however you should keep a coating of oil or grease on these surfaces to prevent excessive wear.
Installation
To ensure long bearing life, make sure your cam followers are properly mounted. A stud type bearing requires a snug fit between the stud diameter and the bore in the support housing. The bearing end plate must be backed up by the support housing face, and both housing faces should be square to the housing bore. Tighten the nut to the torque recommended by the manufacturer. Avoid excessive tightening, as it stretches the stud and shrinks its diameter with consequent loosening in the housing bore.
If you need to mount a stud type cam follower in a blind hole (without nut and lock washer), make sure the stud fits properly in the housing. Use a cam follower with a hex hole so you can tighten the stud enough to achieve good end plate support. A better method is to lock the stud to the housing with a pin, or use setscrews bearing against the stud.
For an eccentric stud bearing, the eccentric bushing must fit loosely in the housing bore so it can be adjusted. The housing must be at least 0.010 in. wider than the bushing length for proper endwise clamping of the bearing. After adjustment is made, you can drill the housing, bushing, and stud for pinning.
Yoke type cam follower bearings also require proper end plate support. Otherwise, they can work off the inner ring. The preferred mounting methods, permit complete axial clamping of the end plates. An alternate method, is acceptable if yoke dimensions are controlled closely, so when the nut is tightened the yoke has enough spring to enable full area clamping of the end plate faces.
Machine Design
3 Comments
Could you offer KRV.19.PP ?
It’s Okay, Steve, I will notice our sales department to contact you~
Like!! Great article post.Really thank you! Really Cool.