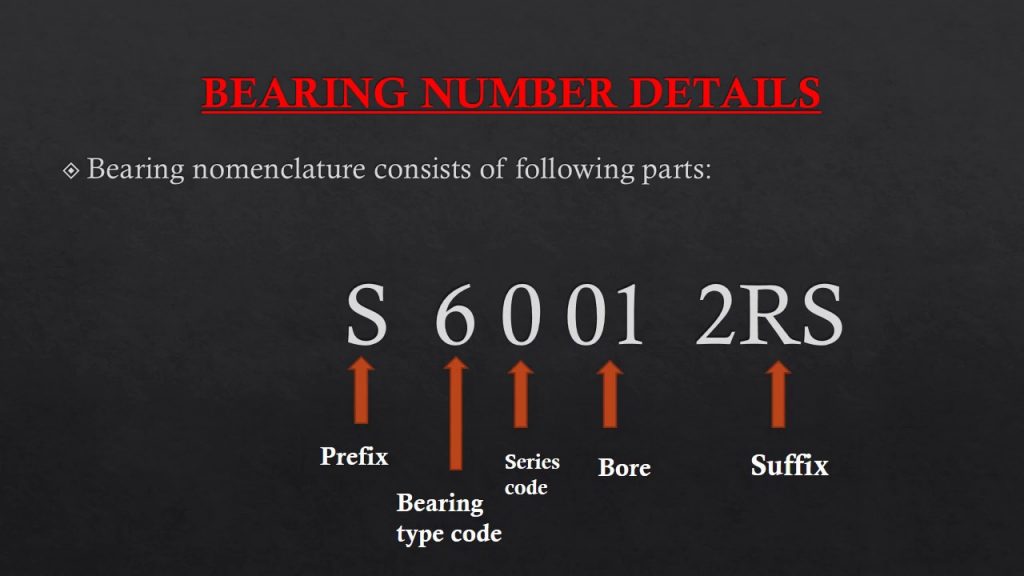
/..: Standardized rolling bearings with uncoded inner diameters
A: Single row angular contact ball bearing with 30° contact angle
AC: Single row angular contact ball bearing with 25° contact angle
ACD: Single row angular contact ball bearing, optimised internal design, 25° contact angle
ADA: Double row full complement cylindrical roller bearing with wide snap ring grooves in outer ring, two inner ring halves held together by U-shaped retaining ring
AS: Needle roller bearing with lubrication hole(s) in outer ring. A figure following the AS indicates the number of holes
ASR: Needle roller bearing with annular groove and lubrication hole(s) in outer ring. A figure following the ASR indicates the number of holes
Axx(x): A combined with a two or three-figure number identifies variants of the standard design, which cannot be identified by generally applicable suffixes
B: Deviating or modified internal design with same boundary dimensions. As a rule the significance of the letter is bound to the particular bearing or bearing series
Examples: 7210 B Single row angular contact ball bearing with 40° contact angle
32210 B Taper roller bearing with steep contact angle (steeper than 32210)
BE: Single row angular contact ball bearing with 40° contact angle and optimised internal design
BEJ: Single row angular contact ball bearing with 40° contact angle and optimised internal design, with ball centred pressed steel cage
BEM: Single row angular contact ball bearing with 40° contact angle and optimised internal design, with machined brass cage
BEP: Single row angular contact ball bearing with 40° contact angle and optimised internal design, with moulded cage of glass fibre reinforced polyamide 66
BEY: Single row angular contact ball bearing with 40° contact angle and optimised internal design, with ball centred pressed brass cage
Bxx(x): B combined with a two or three-figure number identifies variants of the standard design, which cannot be identified by generally applicable suffixes
Example: /B20 Reduced width tolerance
C: 1. Deviating or modified internal design with same boundary dimensions. As a rule the significance of the letter is bound to the particular bearing.
Examples: 7210 C — Single row angular contact ball bearing with 15° contact angle
BSA 205 C — Spherical roller bearing with flangeless inner ring, symmetrical rollers, loose guide ring and pressed steel cage
2. Y-bearing with cylindrical outside diameter, e.g. YET 205 C
CA: 1. Spherical roller bearing of C design, but with retaining flanges on inner ring and machined cage
2. Single row angular contact ball bearing for universal pairing in back-toback, face-to-face or tandem arrangement. When arranged back-to-back or face-to-face there will be a slight axial clearance
CAB: Spherical roller bearing of CA design but with pierced rollers and pin-type cage
CABC: Spherical roller bearing of CAB design but with enhanced roller guidance and correspondingly reduced friction
CAC: Spherical roller bearing of CA design but with enhanced roller guidance and correspondingly reduced friction
CB: Single row angular contact ball bearing for universal pairing in back-to-back, face-to-face or tandem arrangement. When arranged back-to-back or face-toface there will be an axial clearance greater than CA
CC: 1. Spherical roller bearing of C design but with enhanced roller guidance and correspondingly reduced friction
2. Single row angular contact ball bearing for universal pairing in back-toback, face-to-face or tandem arrangement. When arranged back-to-back or face-to-face there will be an axial clearance greater than CB
CD: Single row angular contact ball bearing, optimised internal design, 15° contact angle
CN: Normal internal clearance, normally only used together with a second letter which identifies a reduced or displaced clearance range, sometimes we say C0
Examples: /CNH Upper half of Normal clearance range
/CNM Two middle quarters of Normal clearance range
/CNL Lower half of Normal clearance range
/CNP Upper half of Normal and lower half of C3 clearance
CV: Full complement cylindrical roller bearing with modified internal design
2CS: Sheet steel reinforced rubbing seal of nitrile rubber (NBR) at both sides of spherical roller bearing; a figure following CS indicates a change of design or material, e.g. -2CS2 sheet steel reinforced rubbing seal of fluoro rubber (FPR) at both sides of spherical roller bearing
2CSW: Sheet steel reinforced rubbing seal of nitrile rubber (NBR) at both sides of spherical roller bearing. Without lubrication groove and holes in the outer ring
C1: Bearing internal clearance smaller than C2
C2: Bearing internal clearance smaller than Normal
C3: Bearing internal clearance greater than Normal
C4: Bearing internal clearance greater than C3
C5: Bearing internal clearance greater than C4
A letter (H, M, L or P) following the clearance class is used to indicate that the clearance range is reduced or displaced, see under CN
C01: Reduced running accuracy tolerance range for inner ring
C02: Reduced running accuracy tolerance range for inner ring, smaller than C01
C023: C02 + C3
C03: Reduced running accuracy tolerance range for outer ring
C04: Reduced running accuracy tolerance range for outer ring, smaller than C03
C05: C01 + C03
C06: C02 + C03
C07: C01 + C04
C08: C02 + C04
C083: C02 + C04 + C3
C084: C02 + C04 + C4
D: Deviating or modified internal design with same boundary dimensions; as a rule the significance of the letter is bound to the particular bearing or bearing series
Examples: 3310 D Double row angular contact ball bearing with 45° contact angle; K 40×45×17 D Split needle roller and cage assembly (radial)
DB: Two single row deep groove ball bearings, single row angular contact ball bearings or single row taper roller bearings matched for mounting in a backto-back arrangement; the letter(s) following the DB indicate the magnitude of the axial internal clearance or preload in the bearing before mounting; for paired taper roller bearings the design and arrangement of the intermediate rings between the inner and/or outer rings are identified by a two-figure number which follows immediately after DB
A — Light preload (angular contact ball bearings)
B — Preload greater than A (angular contact ball bearings)
C — Preload greater than B (angular contact ball bearings)
CA — Small axial internal clearance (deep groove and angular contact ball bearings
CB — Axial internal clearance greater than CA (deep groove and angular contact ball bearings)
CC — Axial internal clearance greater than CB (deep groove and angular contact ball bearings)
CG — “Zero” clearance (taper roller bearings)
C… — Special axial internal clearance (the figures following the C give the magnitude of the axial clearance in µm)
GA — Light preload (deep groove ball bearings)
GB — Preload greater than GA
G… — Special preload (the figures following the G give the magnitude of the preload in daN)
DF: Two single row deep groove ball bearings, single row angular contact ball bearings or single row taper roller bearings matched for mounting in a faceto-face arrangement; the letter(s) following the DF are explained under DB
DG: Two single row angular contact ball bearings for universal pairing, i.e. paired for mounting in a back-to-back, face-to-face or tandem arrangement; supplementary designations for axial internal clearance and preload are explained under DB
DH: Single direction thrust bearing with two housing washers
DR: Two single row deep groove ball bearings or cylindrical roller bearings paired to achieve even radial load distribution
DS: 1. Single direction thrust bearing with two shaft washers
2. Split radial needle roller and cage assembly
DT: Two single row deep groove ball bearings, single row angular contact ball bearings or single row taper roller bearings matched for mounting in a tandem arrangement; for paired taper roller bearings the design and arrangement of the intermediate rings between the inner and/or outer rings are identified by a two-figure number which follows immediately after DT
D8: Deep groove ball bearing of open design, also available as standard with shields or seals, but without seal recesses in the outer ring
E: Deviating or modified internal design with same boundary dimensions; as a rule the significance of the letter is bound to the particular bearing or bearing series; usually indicates reinforced rolling element complement
EC: Single row cylindrical roller bearing with optimised internal design
Exx(x): E combined with a two or three-figure number identifies variants of the standard design, which cannot be identified by generally applicable suffixes
F: Machined steel or special cast iron cage; different designs or materials are identified by a figure following the F
FA: Machined steel or special cast iron cage; outer ring centred FB Machined steel or special cast iron cage; inner ring centred
2F: Y-bearing with plain flinger at both sides
G: Single row angular contact ball bearing for universal pairing in a back-toback, face-to-face or tandem arrangement; when mounted back-to-back or face-to-face, the bearing pair will have a small axial clearance
GA: Single row angular contact ball bearing for universal pairing in a back-toback or face-to-face arrangement; when mounted the bearing pair will have a slight preload
GB: Single row angular contact ball bearing for universal pairing in a back-toback or face-to-face arrangement; when mounted the bearing pair will have a preload greater than GA
GC: Single row angular contact ball bearing for universal pairing in a back-toback or face-to-face arrangement; when mounted the bearing pair will have a preload greater than GB
Gxx: Lubricating grease, a second letter after the G indicates the operating temperature range and a third letter identifies the actual grease; the significance of the second letter is as follows:
E — Extreme pressure grease
F — Food compatible grease
H, J — High temperature grease, –20 to +130 °C
L — Low temperature grease, –50 to +80 °C
M — Medium temperature grease, –30 to +110 °C
W, X — Low/high temperature grease, –40 to +140 °C
A figure following the three-letter grease code indicates that the filling degree deviates from the standard: 1, 2 and 3 indicate smaller than standard, 4 to 9 a larger fill
Examples: GEA Extreme pressure grease, standard fill
GLB2 Low temperature grease, 15 to 25 % fill
H: 1. Pressed steel cage (snap-type), hardened
2. Needle roller bearing without inner ring with reduced inside diameter (under rollers) tolerance; followed by tolerance limits in µm, e.g. /H+20+27
HA: Case hardened bearing or bearing component; for closer identification HA is followed by one of the following figures
0 — Complete bearing
1 — Outer and inner rings
2 — Outer ring
3 — Inner ring
4 — Outer ring, inner ring and rolling elements
5 — Rolling elements
6 — Outer ring and rolling elements
7 — Inner ring and rolling elements
HB: Bainite hardened bearing or bearing component; for closer identification HB is followed by one of the figures explained under HA
HC: Hybrid bearing with steel rings and ceramic rolling elements
HE: Bearing or bearing component of vacuum remelted steel; for closer identification HE is followed by one of the figures explained under HA
HM: Martensite hardened bearing or bearing component; for closer identification, HM is followed by one of the figures explained under HA
HT: Grease for high temperatures (–20 to +130 °C), followed by a two-figure number which identifies the actual grease; grease quantities which differ from the standard fill are identified by a letter following HTxx:
A — Grease quantity less than standard
B — Grease quantity greater than standard
C — Grease quantity greater than B
More recently A, B and C have been replaced by F followed by one figure;
F1 = A, F7 = B and F9 = C; the figures have the same significance as those used with the new grease codes Gxx
HV: Bearing or bearing component of hardenable stainless steel; for closer identification HV is followed by one of the figures explained under HA
IS: Needle roller bearing with lubricating hole(s) in inner ring; a figure following; IS identifies the number of holes
ISR: Needle roller bearing with annular groove and lubricating hole(s) in inner ring; a figure following ISR identifies the number of holes
J: Pressed steel cage, unhardened; different designs or materials are identified by a figure, e.g. J1
JHA: Pressed steel cage, hardened, outer ring centred
JR: Pressed steel cage consisting of two flat unhardened washers riveted together (for large thrust bearings)
JW: Pressed steel cage, unhardened, welded
K: Tapered bore; taper 1:12 on diameter
K30: Tapered bore; taper 1:30 on diameter
L: Machined light alloy cage; different designs or materials are identified by a figure, e.g. L1
LA: Machined light alloy cage, outer ring centred
LB: Machined light alloy cage, inner ring centred
LHT: Grease for low and high temperatures (–40 to +140 °C), followed by a twofigure number which identifies the actual grease; grease quantities which differ from the standard fill are identified by a letter following LHTxx, or by Fx as explained under HT
LO: Bearing without preservative, but coated with low viscosity oil; the actual oil is identified by figures following the LO, e.g. LO10
LP: Light alloy window-type cage, with punched or reamed pockets, inner or outer ring centred
LPS: As LP but with lubrication grooves in the guiding surfaces
LS: Land riding seal at one side of bearing; rubbing seal, usually of sheet steel reinforced synthetic rubber, seals against inner ring shoulder
2LS: LS seal at both sides of bearing
LT: Grease for low temperatures (–50 to +80 °C), followed by a two-figure number which identifies the actual grease; grease quantities which differ from the standard fill are identified by a letter following LTxx or by Fx as explained under HT
M: Machined brass cage; different designs or materials are identified by a figure, e.g. M2
MA: Machined brass cage, outer ring centred
MAS: As MA but with lubrication grooves in the guiding surfaces
MB: Machined brass cage, inner ring centred
MBS: As MB but with lubrication grooves in the guiding surfaces
ML: Machined brass window-type cage, inner or outer ring centred
MO: Bearing without preservative, but coated with medium viscosity oil; the actual oil is identified by figures following the MO, e.g. MO10
MP: Machined brass window-type cage, with punched or reamed pockets, inner or outer ring centred
MPS: As MP but with lubrication grooves in the guiding surfaces
MR: Machined brass window-type cage, roller centred
MT: Grease for medium temperatures (–30 to +110 °C), followed by a two-figure number which identifies the actual grease; grease quantities which differ from the standard fill are identified by a letter following MTxx, or by Fx as explained under HT
N: Snap ring groove in outer ring
NR: As N but with snap ring
N1: One locating slot in outer ring
N2: Two locating slots in outer ring at 180° to each other
P: Moulded glass fibre reinforced polyamide 6,6 cage
PH: Moulded cage of polyether ether ketone (PEEK GF16)
PP: Nitrile rubber rubbing seals at both sides of track runner bearing
P4: Dimensional and running accuracy to ISO tolerance class 4 (better than P5)
P4A: Dimensional accuracy to ISO tolerance class 4 and running accuracy to ABMA tolerance class ABEC 9
P5: Dimensional and running accuracy to ISO tolerance class 5 (better than P6)
P6: Dimensional and running accuracy to ISO tolerance class 6 (better than Normal)
P43 — P4 + C3
P52 — P5 + C2
P62 — P6 + C2
P63 — P6 + C3
PA9: Dimensional and running accuracy to ABMA tolerance class ABEC 9 (better than P4)
PA9A: As PA9
PA9B: As PA9 but running accuracy better than ABMA tolerance class ABEC 9
Q: Optimised internal geometry and surface finish of taper roller bearings
QBC: Set of four matched deep groove or angular contact ball bearings; two bearings arranged back-to-back with the other two arranged outside the backto-back pair in tandem with them, i.e. two tandem pairs arranged back-toback
QBT: Set of four matched deep groove or angular contact ball bearings; two bearings arranged back-to-back and the other two in tandem at one side of the back-to-back pair, i.e. three bearings in tandem and back-to-back with fourth bearing
QE5: Special electric motor quality (no longer used)
QE6: Special electric motor quality (no longer used)
QFC: Set of four matched deep groove or angular contact ball bearings; as /QBC but with central pair arranged face-to-face, i.e. two tandem pairs arranged face-to-face
QFT: Set of four matched deep groove or angular contact ball bearings; as /QBT but with face-to-face pair at one side, i.e. three bearings in tandem and faceto-face with fourth bearing
QR: Set of four single row deep groove ball or cylindrical roller bearing matched for equal distribution of radial load
QT: Set of four matched deep groove or angular contact ball bearings arranged in tandem
R: 1. External flange on outer ring
2. Crowned runner surface of support rollers
RF: Rubberised flinger (pressed steel flinger with vulcanised rubber sealing lip) at one side of Y-bearing
RS: Rubbing seal of nitrile rubber at one side of bearing (needle roller bearings)
RS1: Rubbing seal of nitrile rubber with sheet steel reinforcement at one side of bearing
RS1Z: Rubbing seal of nitrile rubber with sheet steel reinforcement at one side and one shield at the other side of the bearing
RS2: Rubbing seal of fluoro rubber with sheet steel reinforcement at one side of bearing
RZ: Low-friction rubbing seal of nitrile rubber with sheet steel reinforcement at one side of bearing
2RF: RF flinger at both sides of Y-bearing
2RS: RS seal at both sides of bearing (needle roller bearing)
2RS1: RS1 seal at both sides of bearing
2RS2: RS2 seal at both sides of bearing
2RZ: RZ seal at both sides of bearing
SM: Needle roller bearing with grease. The two-figure number following identifies the actual grease
SORT: Tolerance grade of needle rollers of a needle roller and cage assembly; the figures following give the actual limits in µm, e.g. /SORT-2-4
SP: Special tolerance class for machine tool spindle bearings; dimensional accuracy approximately to ISO tolerance class 5 and running accuracy approximately to ISO tolerance class 4
S0: Bearing rings (or washers) dimensionally stabilised for use at operating temperatures up to +150 °C
S1: Bearing rings (or washers) dimensionally stabilised for use at operating temperatures up to +200 °C
S2: Bearing rings (or washers) dimensionally stabilised for use at operating temperatures up to +250 °C
S3: Bearing rings (or washers) dimensionally stabilised for use at operating temperatures up to +300 °C
S4: Bearing rings (or washers) dimensionally stabilised for use at operating temperatures up to +350 °C
T: Machined fabric reinforced phenolic resin cage
TA: Machined fabric reinforced phenolic resin cage, outer ring centred
TB: Machined fabric reinforced phenolic resin cage, inner ring centred
TBT: Set of three matched single row deep groove or angular contact ball bearings; two bearings arranged back-to-back and the third in tandem
TFT: Set of three matched single row deep groove or angular contact ball bearings; two bearings arranged face-to-face and the third in tandem
TH: Machined cage of fabric reinforced phenolic resin
TN: Moulded cage of plastic; different designs or materials are identified by a figure following the TN
Example: TN9 Moulded cage of glass fibre reinforced polyamide 66
TR: Three single row deep groove ball or cylindrical roller bearings, matched to give equal distribution of radial load
TT: Set of three matched single row deep groove or angular contact ball bearings arranged in tandem
U: 1. Y-bearing without locking collar
2. Y-bearing locking collar without grub screw
UP: Special tolerance class for machine tool spindle bearings; dimensional accuracy approximately to ISO tolerance class 4 and running accuracy better than ISO class 4
V: Full complement bearing (without cage)
VH: Full complement bearing with non-separable roller complement (cylindrical roller bearings)
VGS: Inner ring raceway of cylindrical and needle roller bearings pre-ground only, for cylindrical roller bearings replaced by /VU001
VU001: Preground raceways
Vxxxx(x): V combined with a second letter and followed by a three or four-figure number identifies variants of the standard design, which cannot be identified by generally applicable suffixes; the second letter identifies a variant group:
Examples: VA — Application oriented variants
VB — Boundary dimension deviations
VE — External deviations and some internal deviations
VQ — Quality, dimensions, accuracy, vibration etc.
VS — Clearance and preload
VT — Lubrication
VA201: Bearing for hot applications (e.g. kiln trucks)
VA301: Bearing for traction motors
VA701: Bearing for papermaking machines
W: Bearing without relubrication facility
W20: Three lubrication holes in outer ring
W26: Six lubrication holes in inner ring
W33: Annular groove and three lubrication holes in outer ring
W33X: Annular groove and six lubrication holes in outer ring
W513: Six lubrication holes in inner ring and annular groove and three lubrication holes in outer ring
W518: Six lubrication holes in inner ring and three lubrication holes in outer ring
W64: “Solid Oil” lubrication
W77: As W33 but with three holes plugged
X: 1. Boundary dimensions altered to conform to ISO standards
2. Cylindrical runner surface (support rollers, cam followers)
Y: Pressed brass cage; different designs or materials are identified by a figure following the Y, e.g. Y1
Z: 1. Combined needle roller bearings with cover
2. Shield (non-rubbing seal) at one side of bearing
2Z: Z shield at both sides of bearing
ZW: Double row needle roller and cage assembly
10 Comments
Damn great!
It looks really good
It’s a great work
It’s great useful for me. Thanks for share.
KEEP FOR USE
Basic but helpful, thanks!
It is very useful.
It’s very great information and I learned from these, will follow in future.
Very useful sharing~
Great 👍