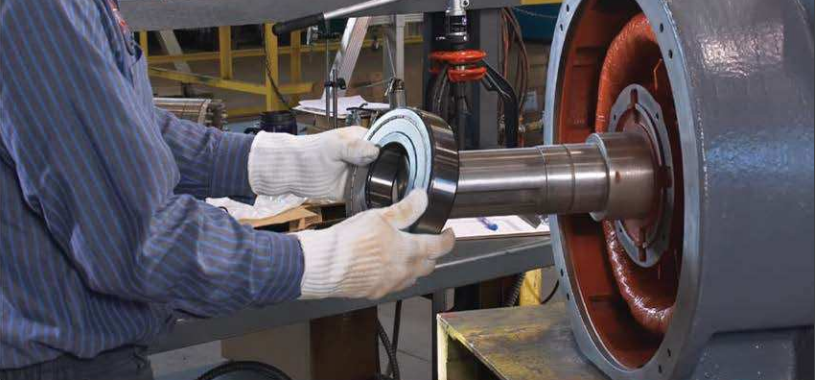
Introduction to Corrective Action Preventive Action (CAPA)
When illness strikes and we need medical attention, we put our trust in the medical products and care givers to provide relief. We expect the care we receive is without fault. Fortunately, failure is not experienced frequently in healthcare and medical devices. When failure does occur, we demand a rigorous process of investigation be initiated to identify why it occurred. Corrective Action Preventive Action (CAPA) is a process which investigates and solves problems, identifies causes, takes corrective action and prevents recurrence of the root causes. The ultimate purpose of CAPA is to assure the problem can never be experienced again. CAPA can be applied in many disciplines. A few of these disciplines are:
- Manufacturing
- Product Design
- Testing Verification and Validation
- Distribution, Shipping, Transport and Packaging
- Use-Applications
What is Corrective Action Preventive Action (CAPA)
Corrective Action Preventive Action (CAPA) is the result of a US FDA requirement, FDA 21 CFR 820.100. The CAPA requirement applies to manufacturers of medical devices and compels them to include CAPA in their Quality Management System (QMS).
CAPA is split between two distinct but related functions.
- Corrective Action (CA) is an extension of Root Cause Analysis (RCA). The first goal of CA is to find the root cause, base event or error that preceded the problem. The second goal is to take action directed at the root cause or error.
- Preventive Action (PA) is similar to Lessons Learned / Read Across. PA resembles the replication activity of Design for Six Sigma (DFSS). Another example of PA in industry is Yokaten, a Japanese term used by Toyota, describing a sharing across the organization. The primary goal of PA is to inform an organization and prevent the problem from returning in other facilities lines or products.
Why Implement Corrective Action Preventive Action (CAPA)
Identifying the root cause of failure is a key tenet of any effective QMS. When a problem occurs, it is often just a symptom of the real issue. Symptoms can be treated but finding out why the symptom is experienced is the true purpose for implementing CAPA. Failure to implement an effective Corrective Action Preventive Action process is a violation of FDA regulations defining Good Manufacturing Practice (GMP).
Once implemented, the CAPA system must exhibit ten objectives to meet the intent of the FDA 21 CFR 820.100 requirement. The 10 objectives of CAPA implementation are:
- Verification of a CAPA system procedure(s) that addresses the requirements of the quality system regulation. It must be defined and documented.
- Evidence that appropriate sources of product and quality problems have been identified.
- Tracking of Trends (which are unfavorable) are identified.
- Data sources for Corrective and Preventive Action are of appropriate quality and content.
- Verify that appropriate Statistical Process Control (SPC) methods are used to detect recurring quality problems.
- Verify the RCA work performed is aligned to the level of Risk the problem has been identified with.
- Actions address the root cause and preventive opportunities.
- CAPA process actions are effective and verified or validated prior to implementation.
- Corrective and preventive actions for product and quality problems are implemented and documented.
- Nonconforming product, quality problems and corrective / preventive actions have been properly shared and included in management review.
How to Implement Corrective Action Preventive Action (CAPA)
There are many ways to apply the two functions of CAPA. The Quality-One Corrective Action Preventive Action approach is as follows:
Corrective Action
When a symptom is observed or communicated, a systematic set of activities are initiated. The activities are intended to describe the problem in sufficient detail so that the team can identify a root cause path. Once a root cause path is selected, a permanent corrective action is identified, verified, implemented and validated. The Quality-One nine-steps for Corrective Action are detailed below:
- Symptom is observed or communicated. The symptom must be quantified through the application of five questions, or 5Q, and confirmed as a true symptom, worthy of defining further.
- Problem Statement is created by using the 5 Why approach, driving as deep into the problem as data will permit.
- Affinity or Ishikawa (fishbone) diagram is used to identify possible causes of the Problem Statement.
- Problem Description is written based on further investigation of the What, Where, When and How Big data collected.
- Possible causes on the Affinity or Ishikawa (fishbone) diagram can then be reduced by using data from the Problem Description.
- Theories are developed on remaining possible causes.
- Root cause is verified by turning it on or off at will.
- Permanent Corrective Actions are determined for root cause and inspection process (which also failed to stop the cause from escaping).
- Implementation and Validation of the Corrective Action.
Preventive Action
Often the root cause of a root cause is the system or lack of policies, practices or procedures which supported the creation of the physical root cause. Preventive Action (PA) occurs after the physical root cause has been identified and permanent corrective action has been validated. PA recognizes the value of the information and actions taken during the CA function. This information is shared within the organization. Quality-One suggests the following steps for Preventive Action:
- Capture the Problem Statement as an Object-Defect for searchable databases.
- Link root causes to the Problem Statement with the Permanent Corrective Action.
- Identify other systems, facilities and processes which could benefit from the knowledge captured.
- Assure Systems Documents are updated, including but not limited to:
- Failure Mode and Effects Analysis (FMEA)
- Control Plan Methodology
- Work Instructions
- Archive information for future retrieval including supporting information.
- Publish and close-out team experience.
Quality One
No Comments