“Bearings are as good as their lubrication”.
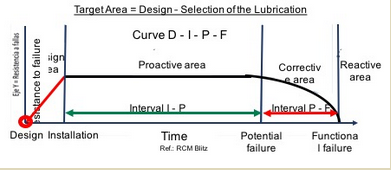
The lubrication is the most important factor for bearing life. Several actual statistics show that incorrect lubrication causes more than 50% of premature bearing failures.A correct lubrication must cover:
1. The correct lubricant. Oil or grease? Viscosity? Temperature range? Anticorrosive properties? EP properties? Consistency of the grease? Etc.
2. The correct lubrication system. Oil: Oil bath? Oil splash system? Circulating Oil? Oil mist? Air-oil? Etc. Grease: Greased for life? Manual relubrication? Automatic centralized system? Automatic lubricators? Etc.
3. Place for the correct application. Oil or grease must be applied in the correct place so that the flow of the lubricant goes correctly to/through the bearings in the most efficient way. Example: The W33 groove with holes in the outer ring of spherical roller bearings.
4. The correct quantity of lubricant. Excess of lubricant may be as bad as to little lubricant. Excess of lubricant will increase the friction and this will increase the operating temperature which will destroy the lubricant. Lack of lubricant will logically not create the required lubricating film and metal to metal contact will take place in between the rolling elements and the raceways of the rings of the bearings.
5. The correct time. The initial lubrication must take place as soon as possible after that the new bearings have been unpacked, thus exposed to the environment.After that, in operation, the lubricant must be renewed or changed while its properties are still acceptable. If the lubricant turns out in bad conditions, there will always already be irreversible damages in the machines!
6. The correct personal. All the persons involved in the lubrication must have been well trained to avoid mistakes. A very simple mistake in the lubrication may close down several machines, or even a considerable part of a plant! Look at the following example: A large size spherical roller bearing 241/900 failed after only 104 hours (4 days!) of operation due to wrong lubrication: Wrong lubricant and wrong lubrication system! A 3.3 tonnes heavy bearing!
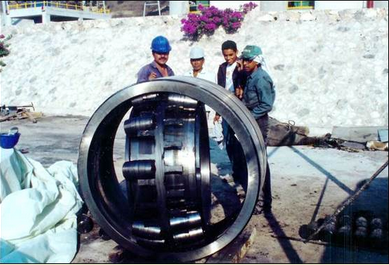
Cost of the replacement bearing: 32,000 Usd. Value of the lost production caused by this failure: 28’000,000 Usd.!
Per Arnold Elgqvist.
BearingXpert
No Comments