Introduction to Six Sigma
In today’s information age, news spreads faster than ever. When an event happens halfway around the world it can become common knowledge within hours or even minutes. Companies must guard their reputation for producing quality products. A single, significant quality incident could result in irreparable damage to brand equity and consumers trust. While there are many quality systems in use today, one methodology has gained tremendous momentum and acceptance throughout industry. The foundational elements of this system can be traced back to the 19th century. In the 1920s, Walter Shewert, a renowned statistician, and sometimes referred to as “the father of statistical quality control”, demonstrated that when process variation reaches three sigma from the mean or average value, the process requires correction. An engineer working for Motorola named Bill Smith later coined the term Six Sigma. Bill Smith, along with Mikel Harry and Bob Galvin, the then CEO of Motorola, developed a new Quality Management System (QMS) that emphasized the relationship between product performance and the corrections required during manufacture. Their four phase system became the basis on which the current Six Sigma methodology was built. The four phases were Measure, Analyze, Improve and Control.
What is Six Sigma
Six Sigma is a system of statistical tools and techniques focused on eliminating defects and reducing process variability. The Six Sigma process includes measurement, improvement and validation activities. The designation, or title, Six Sigma, relates to the connection between the number of defects per million opportunities and the number of standard deviations found within a process specification. Within statistics, sigma is a reference to the intervals under a normal or “Gaussian” curve. Each interval is equal to one standard deviation or sigma. Therefore, Six Sigma refers to the plus or minus three sigma from the mean of the data under the curve. In the case of a normal distribution, 68.26% of the data points are within plus or minus one sigma from the mean, 95.46% are within two sigma and 99.73% are within three sigma. A process variation exceeding ± 3 sigma should be improved. With a Six Sigma capable process, only a very small number of possible failures could fall outside specification limits.
Highly skilled personnel trained in the use of the statistical tools and the techniques of Six Sigma implement the Six Sigma methodologies. The Six Sigma training and certification levels are borrowed from the martial arts. The certification or belt levels include white, yellow, green, black and master black belt designations.
Master Black Belt
A Master Black Belt is classically trained in statistical tools, Six Sigma methodology and management processes. Master Black Belts mentor and direct groups of Black Belts and Six Sigma teams through various problems that need to be reviewed. Additionally, Master Black Belts are responsible for the strategy and training of Black Belt level practitioners and below.
Black Belt
A Black Belt receives the highest level of training in the statistical tools of Six Sigma. Black Belts, as a rule, develop the plans for Six Sigma project implementation. Their responsibilities include creating project plans, leading cross-functional projects and directing team members, including Green and Yellow Belts. Black Belts usually train other team members on the proper use of Six Sigma tools and techniques, such as control charts, histograms and Root Cause Analysis (RCA).
Green Belt
Green Belts report to a Black Belt and lead process improvement teams part time. Approximately 25- 50% of their time should be devoted to working on Six Sigma projects, usually within their own functional areas. Green Belts receive training on DMAIC methodology, statistical tools, proper data collection and analysis of the data collected.
Yellow Belt
A Yellow Belt should have a basic understanding of Six Sigma, statistical tools and DMAIC methodology. Yellow Belts are often members of the workforce recognized for their skill, knowledge and experience with the process in question. They often fulfill the role of Subject Matter Expert (SME) for the process. They are valuable during the measure phase of a project, gathering data, measurements and metrics. However, Yellow Belts are not typically involved in the data analysis process.
Six Sigma is more than a quality system, a set of statistical tools, a certification system or a method for process improvement. Some perceive it as a philosophy that embraces the belief that all business processes are measurable and can be improved.
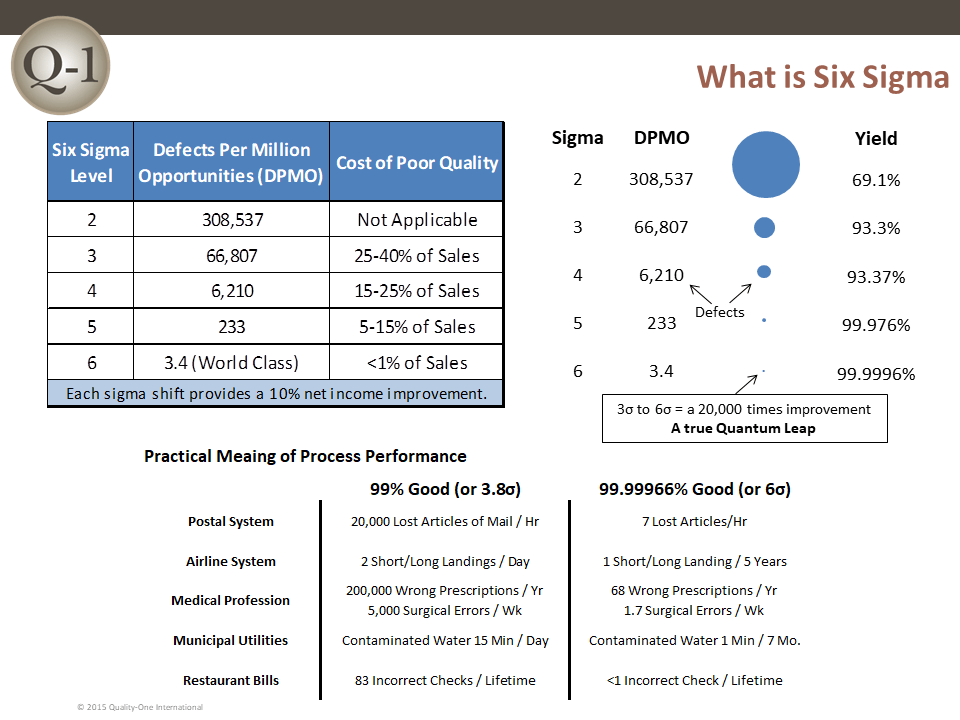
Why Implement Six Sigma
With rising material cost and ever-increasing competition, organizations must seek out methods to increase efficiency. By implementing Six Sigma methodology, an organization can improve efficiency through identification and resolution of product or part defects and minimize the variation within a process. Each Six Sigma project follows a defined sequence of steps and includes specific improvement targets. Some examples could include:
- Reduction in process cycle time
- Reduction of scrap generated by a process
- Increasing customer satisfaction
- Reduction in the number of factory defects
- Reduction or elimination of costly reworks
Every one of the examples listed would have a positive effect on the bottom line of any organization. Six Sigma is not limited to the manufacturing industry. The tools and techniques are currently being used to improve processes in all type of businesses and organizations. The tools can improve manufacturing processes, office or business processes and customer service processes.
How to Implement Six Sigma
A typical Six Sigma project measures the current state and increases the performance of the business process to a new and statistically significant improved state using statistical tools. Standard Six Sigma capability refers to a very small number of possible failures that can exist outside the specification.
The method most frequently associated with Six Sigma is DMAIC, which stands for Define, Measure, Analyze, Improve and Control. Before beginning any Six Sigma improvement project, it is necessary to select a process that, if improved, would result in reduced cost, superior quality or increased efficiency. The process also must possess measurable data because what you cannot measure you cannot improve. The process selected may currently be experiencing quality problems or generating a large amount of scrap.
A Black Belt or Master Black Belt will usually initiate Six Sigma projects through the creation of a charter. The charter typically includes details of the proposed improvement project, a business case and information regarding how the project fits into the company’s goals or business strategy. The following is a list of the project phases, along with a brief description of each:
Define
During the Define phase, the team should complete the following activities:
- Develop a problem statement: The problem statement should contain a clear and concise description of the issue or issues that the project will address. In addition, the statement should include information concerning Critical to Customer Quality (CTQ) requirements (both internal and external), goals and benefits expected through completion of the project.
- Define the Project Scope: The project scope sets the project boundaries. It is essential that the beginning and ending process steps are clearly identified and agreed upon prior to moving forward. Defining the scope will help keep the team focused on the issues at hand and tends to prevent or reduce “scope-creep”.
- Identify Project Resources: Identify the champion, process owner and members of the team along with other resources that may be required on a part-time basis. Management must agree to support the project by committing the resources required for success.
- Develop a Project Plan: The project plan should include a brief statement of how and when the project tasks are to be completed and by whom. In addition, designate the proper lines of communication and intervals of project status updates.
- Develop a High Level Process Map: The high level map of the process is often developed in the SIPOC format which stands for Suppliers, Inputs, Process, Outputs and Customers. Upon completion of the high-level map, the team may select an area for development of a more detailed map.
Measure
During the Measure phase of the project, the team assembles a complete picture of the current state of the process and establishes a baseline through measurement of the existing system. Other activities may include:
- Develop Detailed Process Maps: Develop detailed process maps for high-risk areas of the process, or areas where additional information is required. A detailed process map may reveal process inefficiencies such as long or incorrect cycle times, bottlenecks or non-value added process steps. The process map can also identify where data may be collected.
- Develop Data Collection Plan: Define the methods and objectives of the data collection process. Identify what will be measured, the tools or equipment required, how to measure, how many and how often. In addition, determine the forms that will be used to document the data.
- Validate the Measurement System: A Measurement System Analysis (MSA) may be required to assure that the data collected is accurate. If your data is not accurate you could make decisions based on incorrect information. If Gage Repeatability & Reproducibility (GR&R) is greater than 30%, you may need to make improvements to the measurement system prior to proceeding with data collection.
- Collect the Data: The emphasis during data collection should be gathering data that aids in further defining the problem. In addition, the data should provide information regarding possible causal factors that provide indications of how, when or where the problems occur. In many cases it will be necessary to gather data on process performance over a period of time. One of the key tools for collecting that data is the control chart. The control chart can help identify any trends or outlying measurements.
Analyze
The focus of the Analyze phase is to identify all possible causal factors and determine the root cause of the problem.
- Analyze the Data: The methods used to analyze the data depend on the type of data collected. The data can be analyzed graphically using scatterplots or frequency plots. Statistical analysis should also be performed. In most Six Sigma projects, an Analysis of Variance (ANOVA) is often performed. Other options include Correlation Analysis and Chi-Square testing.
- Identify Causal Factors: This is accomplished using various tools and techniques. One widely used method for gathering and organizing possible causal factors is the Fishbone or Ishikawa diagram. The diagram is often used during brainstorming sessions. The diagram resembles the skeleton of a fish. The main branches of the diagram are usually labeled with the 6Ms: Man, Material, Method, Machine, Measurement and Mother Nature (Environment). The possible causal factors are then listed under each category. The top possible causes derived from the exercise are circled on the diagram and may then be investigated further.
- Determine the Root Cause(s): Often we identify possible causes and implement countermeasures and the problem goes away but eventually returns. This is because we have only treated a symptom of the problem and not the actual root cause. One popular and effective method for determining the root cause is 5 Why and 5 How. The 5 Why method is simply asking the question “Why” enough times until you get past all the symptoms of a problem and down to the root cause. The 5 Hows are used to determine a permanent solution to the root cause(s) of the problem.
Improve
At this point in the project, the team has identified possible root causes of the problem. The Improve phase should identify, implement and validate corrective actions to resolve any process issues and improve performance.
- Identify Potential Solutions: The team should identify possible process improvements that would increase process efficiency, improve quality and operator safety. Brainstorming is commonly used to generate a list of potential solutions. This can be done with a 5 How exercise or close examination of the process maps and statistical analysis results.
- Analyze Failure Modes of Proposed Solutions: Consider reviewing potential improvements for their risk and possible impact on other processes. A Failure Modes and Effects Analysis (FMEA) is often completed prior to implementation of any changes. The FMEA helps the team identify and address potential problems that may arise due to the improvements to the process. If an FMEA already exists for the current process, use it as a baseline and review for changes. The FMEA identifies potential risks along with their severity and likelihood of occurrence. The most critical issues are identified, allowing the team to develop a plan to minimize risk.
- Validate Improvements: Prior to implementation, any process improvement should be validated using statistical methods. The team must verify that the improvement resolved the issue. Validation may be achieved through pilot builds, data collection and analysis and / or creation of a future state process map. The updated map can then be used by the team to perform a Gemba walk of the process and ensure the improvements are completed and implemented correctly.
Control
The objective of the Control phase is to support and maintain the gains realized during the Improve phase. Proper action must be taken to assure the process does not regress back to its previous state. In order to achieve this goal the team will need to take the following steps:
- Update Process Documentation: The team must ensure that all process documentation is updated with the changes to the process due to the improvements implemented. The documents that should be updated include Standard Work, Process Maps, Work Instructions, Control Plans, Visual Aids, etc.
- Associate Training: Assure that all associates are trained on the process and understand the improvements that were introduced and how it affects their responsibilities. The associates should be informed of the purpose of the changes and the benefits of making these changes.
- Implement Statistical Process Control (SPC): SPC will monitor the performance of key steps in the process that relate to the CTQs identified during the Define phase. The control chart should be updated on a regular basis. The associates or process owner should review the charts for any evidence of shifts or trends in the process.
- Create a Process Monitoring Plan: This is one key area where Six Sigma sets itself apart from basic project management The purpose of the monitoring plan is to document how the performance of the process will be monitored over time. The plan should include the metrics that will be monitored, the method of documentation, frequency of measurement and sample size. In addition, the plan should specify who will be notified if there is an issue, the method and timing of the communication, what response is required and who is responsible for executing the response.
- Celebrate: The team should celebrate the successful completion of the project. Management should acknowledge the effort put forth in completing the project and the benefits realized from the project.
Once the Control phase tasks have been completed, it’s time to transfer ownership of the new process to the original process owner. The team should discuss with the champion or Black Belt facilitator any opportunities to carry over the improvements made to other similar processes.
Six Sigma and the DMAIC process work. Many organizations have realized enormous benefits over time. Be careful not to attempt to solve every problem right away, try not to go outside the boundaries of your project scope and do not skip any steps in the process. Trust the process and it will work for you.
Quality One
No Comments