Now we have the correct equipment for the corresponding application and now comes the turn to the installation. An incorrect installation can reduce the useful life of an equipment due to premature failure caused by several defects. The effects are shown in the following graph:
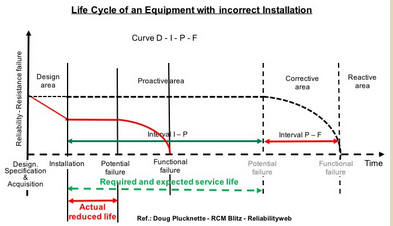
The most common errors in the installation of equipment that reduce the life of the bearings are:
1. Misalignment of the shaft in relation to the driving equipment. Perfectly aligned shafts avoid unnecessary loads on the bearings.It is very easy to detect alignments with vibration analysis and then confirm this cause by means of an analysis of the bearing failure.To avoid this cause of failure there is a large number of aligning instruments on the market that use lasers that are very precise and nowadays very friendly and easy to use without further training.
2. Unbalance. An unbalance also generates unnecessary loads that will cause premature bearing failures. To verify the balance, a vibration analysis must be used, which is able to detect this type of defect very precisely.
3. Mechanical looseness. This problem has increased lately because the designs are increasingly optimized by downsizing, which makes them lighter and less rigid. This defect in the same way can also be detected perfectly well with a vibration analysis.
4. Initial lubrication. In many cases an initial lubrication of the equipment is required before starting them. In this moment of the life cycle of the equipment, several typical errors are also made that reduce the service life of the equipment:
a) Wrong lubricant. The lubricant recommended for the bearings should be checked and checked thoroughly. For this you must review and check at least 5 properties of their properties in relation to the corresponding application.
b) Quantity of the lubricant. It is very common that incorrect amounts are applied from the start of operation of the equipment. For this, the corresponding instructions for each equipment must be verified.
c) Lubrication when it is not necessary. In many cases the equipment is already lubricated by the manufacturer, thus they do not require additional lubrication. An additional lubrication in these cases will generate two defects: Excess lubricant and the possible mixture of incompatible lubricants.
A typical case of this is the type Y Units. These contain bearings that are lubricated by the manufacturer and, in many cases where the applications are not demanding, these do not even require any relubrication during their complete service life.
d) Contaminated lubricants. It must be ensured that the used lubricants are clean. Grease containers that have been open for a long time generally contain fats already in poor condition.
A special case that many ignore are new oils. These oils in no way meet the required cleaning, especially the handling they have suffered before reaching the time of use. No manufacturer certifies the cleanliness of your oil! Therefore, in most cases it is necessary to filter the oils with the correct filters in order to obtain the required service life of the bearings. Fiberglass filters with an efficiency of ß5 = 200 for bearings are recommended.
5. Damages due to bad handling. Direct impacts on to the equipment, especially on the shafts generate internal damages in the bearings that reduce the useful life of these. The most common case is the mounting of the components of the transmissions, either by coupling or belts. There are technics for the mounting of these components that avoid any damage to the bearings and other components.
Please have in mind my message:
“Impacts on the balls hurt!” The above is explained in detail in my courses, specially in courses on site, as these are designed according to the priorities and specific needs of the corresponding Customers! Please let me know if you are interested!
Per Arnold Elgqvist.
BearingXpert
2 Comments
Informative article, just what I was looking for.
Thank you Kitana, we are glad that our articles are useful~